What does IQ OQ and PQ mean? Why is it Critical in Pharma – A Practical Guide with Real-World Examples
By: Gerry Creaner B.Chem Eng. and Donagh Fitzgerald B.Prod Eng. Last Updated: February 2025
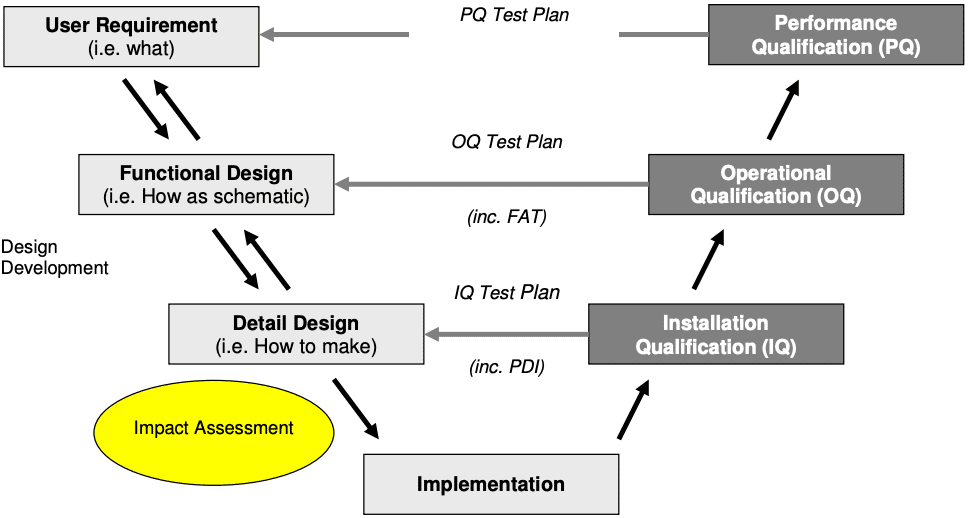
What does IQ OQ and PQ mean?
In regulated industries like pharmaceutical and medical device manufacturing, ensuring that equipment and systems function as intended is critical for compliance, safety, and product quality.
This is where IQ OQ PQ – short for Installation Qualification, Operational Qualification, and Performance Qualification – come into play. These are 3 distinct steps used to confirm that the equipment, piping, instruments, and utilities (like air, water, and steam) used in a pharmaceutical factory are:
- Installed correctly (IQ)
- Operate as intended (OQ)
- Perform consistently under real working conditions (PQ)
The purpose of IQ OQ PQ is to confirm everything works as intended and to create a documented evidence trail that proves to the owners/clients or the regulatory agencies that have jurisdiction over that facility that everything meets both regulatory and operational requirements.
This evidence trail can be on paper or electronic and must include signatures from individuals in key departments, such as Validation, Engineering, Maintenance, Calibration, Quality Assurance, etc.
IQ OQ PQ Training Course
BTW, if you need to learn how to populate an IQ IQ PQ equipment qualification protocol, check out our Equipment Validation (IQ OQ PQ) Training Course – For Starter Validation, CQV and C&Q Roles.
1) Installation Qualification (IQ)
- The first step.
- Checks that the equipment, piping, and components are:
- Delivered correctly.
- Installed properly.
- Configured to meet the manufacturer’s or approved standards.
- Achieves this by comparing the design specifications (“what was specified”) to the actual on-site conditions (“what was found”).
2) Operational Qualification (OQ)
- Follows IQ.
- Tests if the equipment and systems work as expected. For example:
- Does it run at the right speed?
- Does it heat or cool to the right temperature?
- Is the motor moving in the correct direction?
- Confirms the equipment operates within the limits set by the manufacturer.
3) Performance Qualification (PQ)
- Comes after IQ and OQ.
- Confirms the equipment is fit for its intended use as described in the User Requirements Specification (URS).
- Tests the equipment under actual working conditions to make sure it performs as required.
What is an IQ OQ PQ Protocol?
An IQ OQ PQ Protocol, a written plan that outlines how there 3 qualification steps will be executed. The protocol is written for each critical system within the manufacturing environment. It ensures that no critical steps are missed and help confirm that the equipment is fit for use, safe, and compliant with required standards.
Each of these steps (IQ, OQ, and PQ) can be also be documented as a standalone protocol or combined (i.e. IQ and OQ can be combined into IOQ. In other situations, PQ may be combined with OQ or combined with Process Validation or Process Performance Qualification). However, in every case, the protocols need to be prepared specifically for the system or equipment being qualified.
The protocol includes the specific test parameters, component-level impact assessments, product characteristics, production equipment, the procedures to be followed, the expected outcomes, and the acceptance criteria.
When populating and executing the protocol, all actions, tests, results, and any deviations from the expected outcomes must be documented carefully. This is crucial for regulatory compliance and for audits by agencies like the FDA or EMA.
Jump to section
Why do we need Qualification (IQ OQ PQ)?
Two main reasons.
1. It’s a regulatory requirement
According to the Food and Drug Administration (FDA)
“Equipment used in the manufacture, processing, packing, or holding of a drug product shall be of appropriate design, adequate size, and suitably located to facilitate operations for its intended use and for its cleaning and maintenance.” – 21 CFR Title 211.63,
While the FDA mandates equipment qualification, it doesn’t provide specific methods for how to conduct the process. It’s up to each company to ensure their equipment is designed, cleanable, and maintainable, and to demonstrate its fitness for purpose.
In the EU, EudraLex – Volume 4 – Good Manufacturing Practice (GMP) provides more detailed guidance on qualification under Annex 15: Qualification and Validation
And while not regulation, ISPE Baseline Guide 5 Commissioning and Qualification (Second Edition) is a widely used guide in qualification that enjoys the support of numerous regulatory authorities.
2. Product Quality and Patient Safety
Even small errors in equipment installation or performance can have serious consequences in pharmaceutical manufacturing. Minor issues, especially in new or untested systems, can escalate and lead to major product quality problems or even patient harm.
IQ, OQ, and PQ are used to:
- Create documented proof that systems are installed and operate according to specifications, ensuring consistent, reliable performance.
- Prevent errors during installation, operation, and performance testing.
- Ensure reliable equipment operation, leading to consistent production of safe, high-quality products.
What is Installation Qualification (IQ)?
Installation Qualification (IQ) is a documented process that ensures critical equipment, piping, software, or instruments that directly affect product quality have been:
- Properly delivered: You were shipped exactly what you ordered
- Correctly installed: Confirming installation meets required standards.
- Configured appropriately: Following the manufacturer’s guidelines or an approved installation checklist.
Think of IQ as a thorough check to confirm that installed equipment meets design specifications and is set up correctly.
For example, if you’ve installed a new pressure vessel, IQ verifies that:
- The manufacturer shipped you the right piece of equipment.
- It’s made from the right materials as per the design specifications.
- It’s installed in the proper location.
- The piping, instrumentation, and electrical wiring are connected properly.
Who Performs IQ?
IQ is conducted by Commissioning, Qualification, and Validation (CQV) engineers and technicians or Validation engineers and technicians.
Typical IQ Activities
These include:
- Delivery Checks:
- Verifying received items against the packing list.
- Checking for shipping damage.
- Specification Verification:
- Confirming the manufacturer’s technical specifications match design and operational requirements.
- Identifying and verifying serial numbers, make, and model for all components.
- Installation Verification:
- Ensuring the correct equipment is installed in the right location.
- Checking piping, wiring, and connections to other units or equipment.
- Inspecting secondary instruments and ancillary equipment.
- Verifying proper energy or utilities supply.
- Confirming environmental and operating conditions meet the manufacturer’s guidelines.
- Software and Documentation:
- Verifying software installation.
- Recording firmware versions and serial numbers.
- Logging calibration and validation dates of equipment used for the qualification.
- Collecting all relevant documentation, such as manuals, calibration certificates, and certificates of conformity.
Documentation and Approval
The entire IQ process is documented using pre-approved checklists. Each checklist is signed by the individual performing the procedure and then reviewed and approved by a senior validation peer and a quality assurance representative.
Layout of an IQ checksheet for equipment installation
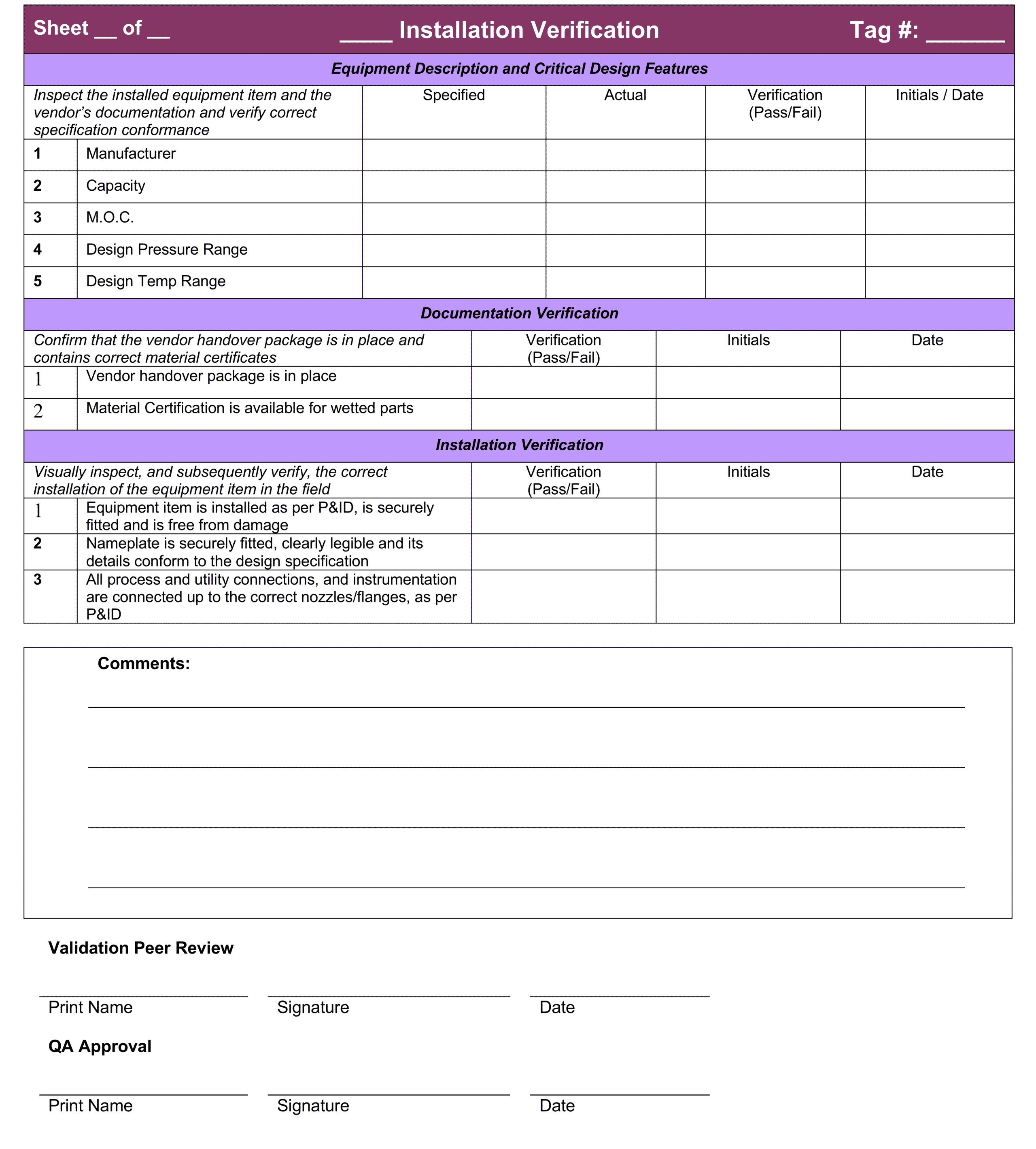
IQ Templates
Click here for some more examples of professional IQ Templates for equipment installation verification, instrument installation verification, piping instrumentation verification and a P&ID walkdown template.
Example 1:
A pharmaceutical company installs a new CIP system for cleaning stainless steel mixing tanks used in biologics manufacturing. During IQ, the validation team checks:
- That all piping and spray balls are installed per the Process & Instrumentation Diagram (P&ID).
- That the detergent and rinse solution supply lines are connected properly.
- That pressure and flow rate sensors are installed in the correct locations.
- That the system passes a dry run with water to confirm no leaks.
If the system fails IQ (e.g. a pump is installed backward, or a flow sensor is missing), these issues must be documented and fixed before moving to OQ.
Example 2:
A pharmaceutical company installs a new autoclave for sterilizing glass vials. During IQ, the validation team checks:
- The autoclave’s model and serial number match the purchase order.
- It is installed on a level surface, as per manufacturer requirements.
- Electrical and steam connections meet the required voltage and pressure.
- All manuals, certificates, and calibration records are in place.
If any issue arises (e.g. incorrect wiring or missing documentation), it must be documented and addressed before moving to the next phase.
What is Operational Qualification (OQ)?
Operational qualification is a documented testing process to make sure that the equipment and systems operate as defined in the design stage and are within the operating ranges listed by the manufacturer.
This is the next step after IQ and confirms that the equipment operates as intended.
To conduct OQ, Commissioning and Qualification (C&Q) engineers collaborate with maintenance staff and engineers from various disciplines, including process, chemical, automation, instrumentation, and mechanical. They follow a detailed test plan to:
- Test the equipment.
- Document the results.
- Compare and verify performance against the design specifications.
What are OQ Tests?
Features commonly tested in OQ include:
- Temperature Control Systems
- Overheating/Low-Temperature Alarms
- Pressure Control Systems
- Fan/Motor Speed (RPM)
- Display Units/Human-Machine Interface (HMI)
- Operational Signals
- Servo Motor Accuracy
- Pressure Switches
- Level Switches
Testing Methods
- Simple Tests:
- Sending power to the equipment.
- Opening and closing ports and valves to verify signal and switch functionality.
- Checking components for proper operation.
- Complex Tests:
- Pressure tests.
- Flow tests.
- Equipment interlock testing.
- Speed tests.
Example 1:
The same pharmaceutical company runs OQ tests on the newly installed CIP system:
- A riboflavin test is performed by spraying fluorescent dye inside the mixing tank, running the CIP cycle, and inspecting for residues under UV light.
- Flow sensors confirm that detergent and rinse water circulate at the correct velocity (e.g. 1.5 meters per second) to remove residues.
- The temperature of the hot water rinse is monitored to ensure it reaches 85°C.
- The control system is tested by introducing intentional errors (e.g. disconnecting a detergent line) to verify that alarms trigger correctly.
If flow rates are inconsistent or spray coverage is incomplete, adjustments (e.g. increasing pump speed or repositioning spray nozzles) are made before moving to PQ.
Example: 2
After completing IQ, the same autoclave undergoes OQ testing. The team:
- Runs empty cycles to confirm the correct sterilization time, pressure, and temperature.
- Tests alarm systems by introducing intentional errors (e.g. low steam pressure).
- Verifies that the control panel responds as expected.
If the sterilization cycle takes longer than expected, adjustments may be needed before proceeding to PQ.
What is Performance Qualification (PQ)?
Performance Qualification (PQ) confirms that equipment and systems meet the user’s needs and are suitable for their intended use, as defined in the User Requirements Specification (URS). It is the final step in equipment qualification.
How PQ Differs from OQ
While similar to Operational Qualification (OQ), PQ tests the equipment under real-world conditions, meaning it operates with a load or process medium, replicating the actual conditions it will experience during production.
What are PQ Tests?
Features commonly tested in PQ include:
- Excessive vibration or noise: Caused by resonance when multiple vibrating components interact.
- Overheating: Often due to improperly aligned or tensioned driving belts.
- Process media backflow: Resulting from incorrectly sized or installed pipework.
- Pressure differentials: Caused by issues like faulty valves, other equipment, or backflow.
- Compound faults: Small issues combining to create significant operational problems.
- Operational inconsistencies: Variability in performance during processes such as mixing, blending, or granulation.
- Product quality issues: Including chemical impurities, incorrect particle sizes, or problems with content uniformity.
Key Focus of PQ
- Ensures the equipment performs consistently and reliably under actual production conditions.
- Identifies and resolves any operational issues that could affect product quality or process efficiency.
- Verifies that the system as a whole meets the defined specifications and requirements.
Performance Qualification must not be confused with Process Validation (PV) (verification that good product is made) or with cleaning validation and analytical methods.
Example 1:
The company performs PQ on the CIP system by running it under actual production conditions:
- Tanks used for vaccine formulation are cleaned after batch production.
- Post-cleaning swab tests check for residual proteins, endotoxins, and microbial contamination.
- Rinse water samples are analyzed for detergent residues to ensure no carryover.
- Cleaning cycles are repeated three consecutive times, confirming reproducibility.
If one batch fails (e.g. detergent residue is found in rinse water), cycle parameters (e.g. rinse duration or flow rate) may need optimization.
Example 2:
The autoclave is now tested with actual vials filled with liquid medication. During PQ, the team:
- Loads the autoclave with vials as per routine production.
- Runs sterilization cycles while measuring key parameters (temperature, pressure, exposure time).
- Collects data from biological indicators (BIs) placed inside test loads to confirm sterility.
- Repeats the test three times to ensure consistency.
If the vials consistently pass sterility testing, the autoclave is validated for routine use.
Where is IQ OQ PQ Used?
Here are some examples of places where IQ OQ PQ might be used throughout the manufacturing process…
1. Process Equipment Qualification
- Bioreactors & Fermenters – Ensuring they are installed correctly (IQ), function as required (OQ), and produce consistent batches (PQ).
- Mixing Tanks & Blenders – Verifying uniform mixing for drug formulations.
- Tablet Press Machines – Ensuring consistent tablet weight, hardness, and dissolution rates.
- Capsule Filling Machines – Checking for proper filling accuracy and integrity of capsules
2. Clean-In-Place (CIP) & Steam-In-Place (SIP) Systems
- Ensuring that cleaning and sterilization systems effectively remove contaminants.
- IQ verifies installation, OQ ensures correct operation (e.g., flow rates, temperatures), and PQ confirms repeatability and effectiveness of cleaning cycles.
3. Sterilization & Aseptic Processing Equipment
- Autoclaves – IQ ensures proper installation, OQ confirms sterilization parameters (e.g., temperature, pressure, time), and PQ demonstrates effective microbial load reduction.
- Depyrogenation Tunnels & Ovens – Used for glass vials, syringes, etc., to remove endotoxins.
- Lyophilizers (Freeze Dryers) – Ensuring correct freeze-drying cycles for biologics and injectables.
4. HVAC & Environmental Control Systems
- Cleanroom qualification, including air handling units, HEPA filters, and differential pressure controls.
- Ensuring controlled temperature, humidity, and particle levels in classified areas.
5. Water & Utility Systems
- Purified Water (PW), Water for Injection (WFI), & Clean Steam Systems – Ensuring water quality meets pharmacopeial standards.
- Compressed Air & Nitrogen Systems – Used in aseptic environments and direct product contact applications.
6. Analytical & Laboratory Equipment
- HPLC (High-Performance Liquid Chromatography) Systems – Ensuring accurate and reproducible analytical results.
- Spectrophotometers & TOC Analyzers – Used for quality control testing.
7. Packaging & Serialization Equipment
- Blister Packaging & Bottle Filling Lines – Ensuring correct dosing, labeling, and integrity.
- Track & Trace Systems – Validating serialization for regulatory compliance (e.g., EU FMD, US DSCSA).
What is the V-Model for Direct Impact Systems?
The V-model is a method used to visualize and compare the relationship between the user requirements, functional design and detailed design to the installation qualification (IQ), operational qualification (OQ) and performance qualification (PQ) performed on them (see diagram below).
To implement, you start at the top left with developing user requirements, work down the left hand side of the V, and then up the right hand side, ending at PQ.
The left-hand side of the V represents what you want the system to do and how you’ll achieve that. The right-hand side of the V represents how you test the system to confirm that the system is fit-for-purpose (i.e. will make safe medicines for patients).
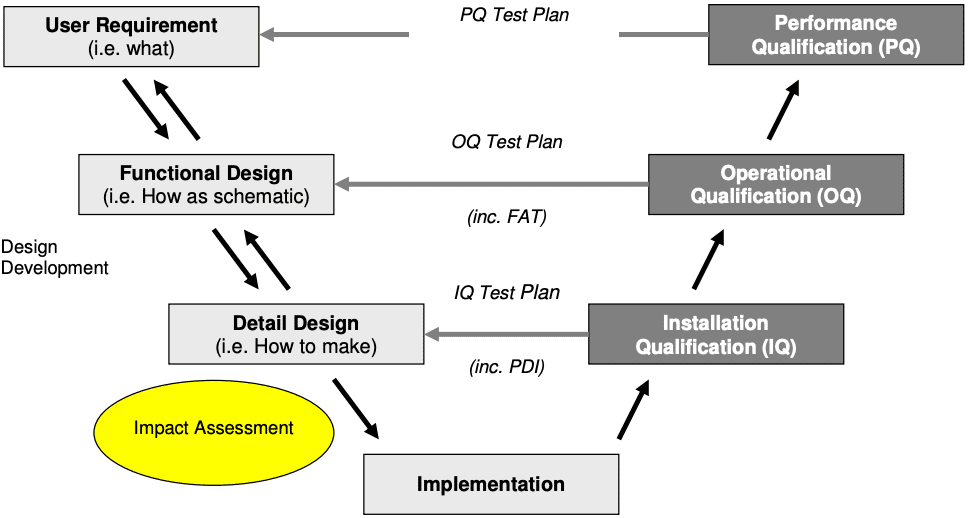
In pharmaceutical manufacturing, most companies and organisations follow the ISPE’s V-Model (ISPE Baseline Guide Volume-5) to validate their systems as it meets the requirements of the industry regulators such as the Food and Drug Administration (FDA) or the European Medicines Association (EMA).
What is an Equipment Qualification Protocol?
Always Remember!
- The goal is to make safe medicines at an affordable cost – you must balance these objectives. There can be a tendency (especially amongst novice C&Q technicians and engineers) to qualify all components in a system. However, the qualification process is enormously time-consuming and expensive so this approach drives up the cost of qualifying and validating the project. In turn, the final price of medicine becomes way higher than necessary (potentially even making it unaffordable to less well-off patients). The solution is to use system impact assessments, component impact assessments and risk management tools in a scientifically robust manner to support your decisions about what to validate. This helps to avoid over-qualifying.
- Use commissioning data wherever possible to reduce testing duplication. The quality assurance department will need to approve.
- There is no single right answer or a “perfect” approach to validating a project. In fact, there are always multiple right answers and approaches. The key point is that you must be able to explain your rationale to an FDA or EMA auditor or supervisor. What you’re looking to demonstrate is sound and logical rationale for your decisions so that even if someone disagrees with you, they can understand the decision, you won’t be penalised (even if you are asked to change it).
Next Steps
If you need to learn how to populate an Equipment Validation Protocol, check out our Equipment Validation (IQ OQ PQ) Training Course – For Starter Validation, CQV and C&Q Roles where we walk you through this entire qualification process step by step.
About the Authors
Gerry Creaner
President
Senior Lecturer with GetReskilled
Gerry Creaner has over 30-years of experience in the Life Sciences Manufacturing industry across a range of technical, managerial and business roles. He established a very successful engineering consultancy prior to founding GetReskilled, an online education and learning business, with offices in Singapore, Ireland and Boston (USA), focussed on the manufacture of safe and effective medicines for the public.
He is also a founding Director of two Singapore based philanthropic organizations, the Farmleigh Fellowship and the Singapore-Ireland Fund, both of which deepen the well established and historical Singapore – Ireland relationship and deliver long-term benefits to both countries.
Gerry has an undergraduate degree in Chemical Engineering (UCD, 1980) and an MSc (Management) from Trinity College Dublin (2003) and is currently doing research for his Ph.D.
Donagh Fitzgerald
Head of Marketing & Product Development
Mechanical/Production Engineer
Donagh looks after the marketing and product development including the training and pedagogical elements of our programs and makes sure that all GetReskilled’s users can have a great online learning experience. Donagh has lived and worked in many countries including Ireland, America, the UK, Singapore, Hong Kong and Japan. Donagh has also served as the Program Manager for the Farmleigh Fellowship based out of Singapore.
Donagh holds Degrees in Production Engineering and Mechanical Engineering from South East Technological University, Ireland.